Xingke Group Takes Root in East China: 30,000-Square-Meter Steel Pipe Manufacturing Base Begins Production, Setting a Benchmark for High-End Tubular Product Full-Industry-Chain
Mar.03.2025
(Qingdao, China, June 10, 2024) Amid the tide of the "dual circulation" strategy and the intelligent upgrading of the manufacturing industry, Xingke Group announced that its high-end steel pipe manufacturing subsidiary in Qingdao, Shandong, has officially entered full operation. The base, which began construction in 2022, covers an area of 30,000 square meters (equivalent to four standard football fields). It is equipped with two seventh-generation intelligent pipe-making units developed by a well-known local equipment manufacturing enterprise in Qingdao. The facility can produce precision round pipes with diameters ranging from 30 to 273 mm and wall thicknesses from 2.0 to 6.0 mm, as well as custom square pipes ranging from 30×30 mm to 200×200 mm, with an annual production capacity exceeding 150,000 tons. This move marks a key step in Xingke Group's strategic transformation from a "product supplier" to an "industry chain integrator."
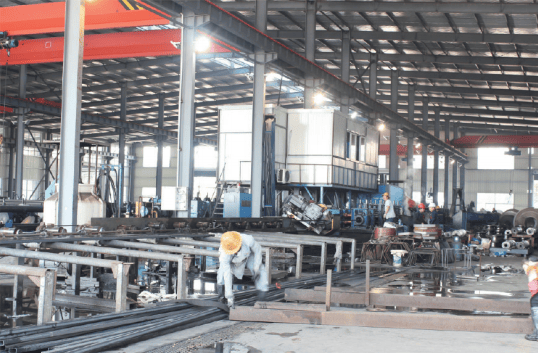
Breaking the High-End Tubular Products Bottleneck: A New Benchmark for Domestic Intelligent Manufacturing
China, the world's largest steel pipe producer, has long relied on imports for high-end precision tubular products. Specialized tubular products, such as those used in new energy photovoltaic (PV) supports and semiconductor equipment frames, have stringent requirements for dimensional accuracy, surface finish, and mechanical properties. Domestic equipment previously struggled to break through the ±0.1 mm precision limit.
The commissioning of Xingke's Qingdao base directly addresses this challenge. The pipe-making units, equipped with laser dynamic alignment systems and AI vision quality inspection modules, can achieve straightness errors of ≤0.05 mm/m and weld seam strength exceeding 98% of the base material, matching the standards of German and Japanese counterparts. "Our round pipes have a wall thickness uniformity variation controlled within 3%, and the diagonal tolerance of square pipes is 30% better than national standards," said Zhao Qiming, General Manager of Xingke's Pipe Division, while showcasing the first batch of samples at the commissioning ceremony. "This means that domestic PV support pipes can finally replace imported products, with costs reduced by 25%."
Dual-Machine Synergy: A Leap from Construction Pipes to Precision Tubular Products
The core equipment of the base consists of two "twin-star" pipe-making machines:
- Canglong-H90 High-Frequency Welded Pipe Unit: Specializing in large-diameter tubular products for construction structures and mechanical manufacturing, it employs dual-seam penetration technology with a maximum pipe-making speed of 60 meters per minute. It can produce 273 mm ultra-large-diameter round pipes, filling a gap in the East China region.
- Qingluan-P20 Precision Cold-Bending Forming Unit: Focusing on high-end fields such as new energy and automotive industries, it features a zero-oil electrostatic spray coating process for inner wall treatment, achieving seamless corners in 200×200 mm square pipes through a single cold-bending process, meeting the requirements of semiconductor cleanrooms.
"The combination of these two machines enables Xingke to serve both the traditional infrastructure 'mainstay' and the 'gold rush' of emerging industries," commented Liu Zhenye, President of the Qingdao Equipment Manufacturing Industry Association. Currently, the base has signed annual framework agreements with three domestic PV leaders for 2024, with high-end tubular product orders expected to exceed 40%.
Green Intelligent Manufacturing: Xingke's Solution to Reduce Carbon by 12 kg per Ton of Steel Pipe
Driven by the dual-carbon goals, the base has innovatively built a "green pipe-making" full chain:
- Intelligent Energy Conservation: The units are equipped with a waste heat recovery system that converts the heat generated by high-frequency welding into workshop heating, reducing energy consumption by 18%.
- Circular Regeneration: Water-based environmental passivation liquids replace traditional chromic acids, reducing waste liquid treatment costs by 50%, with 100% recyclable tubular products.
- Digital Twinning: Virtual factory simulation optimizes production parameters, reducing trial production waste by over 800 tons annually.
According to estimates, Xingke's steel pipes have a carbon footprint per ton that is 12 kg lower than the industry average, equivalent to planting 26,000 trees annually.
Industry-Research Integration: Building a "Future Tubular Products Laboratory" with Universities
Conclusion: The Fable of Industrial Upgrading in a Steel Pipe
From scaffolding on construction sites to floating offshore PV arrays, from battery supports for new energy vehicles to components in space station experimental cabins, every steel pipe from Xingke's Qingdao base tells the story of the evolution of Chinese manufacturing from "big" to "strong." As Jin Baotai, Chairman of Xingke Group, said at the commissioning ceremony, "These 30,000 square meters are not just a production workshop but also a testing ground for China's independent high-end equipment. When our steel pipes can support the most precise PV power stations, the backbone of Chinese intelligent manufacturing will be strong enough to stand tall."